High-output injection molding services provide efficient production solutions for high-precision plastic parts, suitable for various sectors including automotive, consumer goods, medical, and electronics. This process utilizes advanced technologies to optimize cycle times and reduce costs, supporting rapid prototyping and market responsiveness. Emphasizing automation and real-time data monitoring, these services enhance operational efficiency while ensuring quality control through rigorous testing and monitoring protocols. The ability to adjust production volumes in line with market demand positions businesses for competitive advantage. For further insights into advancements and application potentials, consider exploring the technology and methodologies driving success in this field.
Understanding High Volume Injection Molding
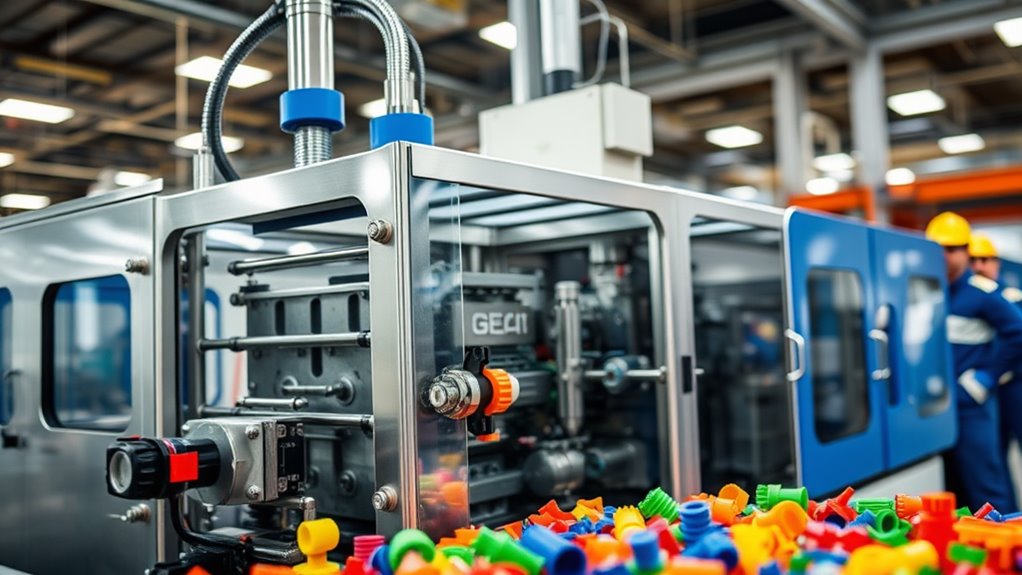
High volume injection molding is a manufacturing process characterized by the rapid production of large quantities of plastic parts with high precision and consistency. This technique leverages advanced machinery and technology to achieve exceptional production speed, enabling manufacturers to meet increasing market demands efficiently.
The process involves injecting molten molding materials into a precisely engineered mold, allowing for intricate designs and complex geometries.
The selection of molding materials is critical, as it directly influences the quality and functionality of the final product. Commonly employed materials include thermoplastics and thermosetting polymers, each offering unique properties tailored to specific applications. The ability to utilize a diverse range of molding materials enhances the versatility of high volume injection molding, accommodating various industries from automotive to consumer goods.
Furthermore, the integration of automation and real-time monitoring systems elevates production efficiency and minimizes defects. By optimizing parameters such as temperature, pressure, and cycle times, manufacturers can considerably reduce production costs while maintaining stringent quality standards.
As industries continue to evolve, high volume injection molding remains a cornerstone of innovation, driving advancements in product development and manufacturing capabilities.
Benefits of High-Output Services
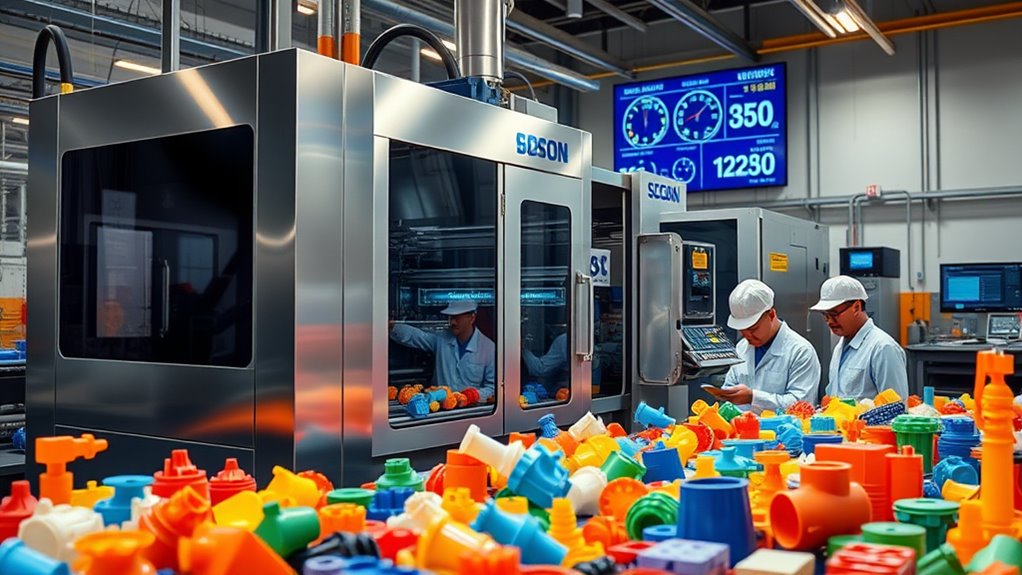
The advantages of high-output injection molding services are significant, particularly in today’s fast-paced manufacturing environment. One of the primary benefits is cost efficiency. By maximizing the number of parts produced in each cycle, manufacturers can reduce the cost per unit, thereby enhancing profitability. This efficiency is achieved through optimized processes and advanced machinery that minimize waste and downtime, ensuring that resources are utilized effectively.
Another essential advantage is production speed. High-output services can drastically reduce lead times, enabling companies to respond swiftly to market demands. With the ability to produce large volumes quickly, businesses can maintain competitive advantage by ensuring timely delivery of products to customers.
This rapid production capability also allows for increased flexibility in inventory management, as manufacturers can ramp up or scale back production in response to fluctuations in demand.
Furthermore, high-output injection molding services facilitate innovation by enabling the rapid prototyping of new designs. This agility not only fosters creativity but also supports the development of more complex and refined products.
To summarize, the benefits of high-output injection molding services lie in their ability to deliver cost efficiency and enhanced production speed, vital for businesses aiming for success in a dynamic marketplace.
Key Technologies Used
As manufacturers seek to enhance the efficiency and quality of high-output injection molding services, several key technologies have emerged as pivotal in this endeavor. One of the most significant advancements is the implementation of automation technologies, which streamline production processes and reduce cycle times.
Automated systems facilitate precise control over molding parameters, ensuring consistent product quality while minimizing waste.
Moreover, the integration of advanced materials and design software enables the production of lightweight, high-strength components that meet modern engineering demands. These innovations not only improve performance but also align with sustainability practices by reducing material consumption and energy use during production.
In addition, real-time monitoring and predictive maintenance technologies are transforming operational efficiency. By leveraging data analytics, manufacturers can anticipate equipment failures and optimize maintenance schedules, thereby enhancing uptime and productivity.
Finally, the adoption of environmentally friendly materials, such as bio-based plastics, supports sustainability efforts within the industry.
These technologies collectively drive the evolution of high-output injection molding services, aligning profitability with ecological responsibility and positioning manufacturers at the forefront of innovation.
Applications Across Industries
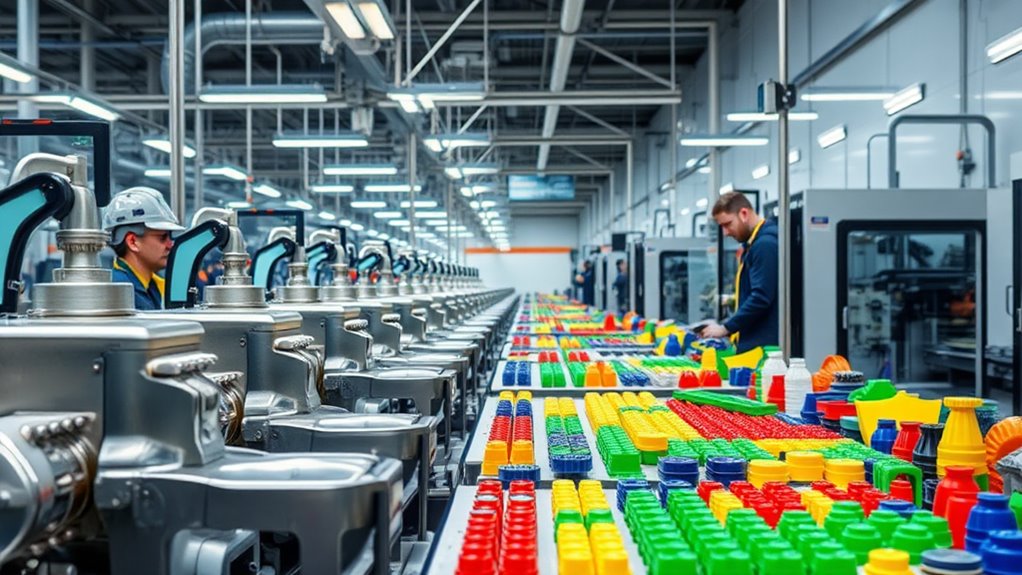
While high-output injection molding services are mainly recognized for their role in the manufacturing sector, their applications extend across a diverse range of industries, including automotive, consumer goods, medical devices, and electronics.
In the automotive sector, high-output injection molding is essential for producing complex automotive components with precision and efficiency. These components, ranging from interior panels to intricate engine parts, benefit from the rapid production capabilities of this technology, ensuring that manufacturers can meet tight deadlines and stringent quality standards.
In the sphere of consumer products, high-output injection molding facilitates the creation of innovative and durable items, from household goods to packaging solutions. The ability to mold intricate designs with various materials allows for customization and enhancement of product functionality, appealing to consumer preferences for aesthetics and usability.
Additionally, the scalability of high-output processes supports mass production, enabling companies to respond dynamically to market demands.
The versatility and efficiency of high-output injection molding services position them as a crucial component across industries, fostering innovation and driving advancements in product design and manufacturing methodologies.
Quality Control Measures
Z:\Zimmwriter\HighOutput_Injection_Molding_Services_0005.jpg
Ensuring product integrity and operational excellence hinges on robust quality control measures in high-output injection molding services. These measures are paramount in maintaining high standards of quality assurance, which is critical for meeting stringent industry regulations and customer expectations.
Quality control begins with material selection, where advanced analytics are employed to assess the properties of polymers, ensuring compatibility with design specifications.
Throughout the production process, real-time monitoring systems are implemented to track key parameters such as temperature, pressure, and cycle times. This data is essential for process optimization, allowing manufacturers to identify deviations and make immediate adjustments.
Moreover, post-production inspections utilize sophisticated techniques such as automated vision systems and non-destructive testing to evaluate the integrity of molded parts.
Statistical process control (SPC) further enhances quality assurance by applying statistical methods to monitor and control the manufacturing process.
What Volumes Are REalistic For High -Volume Injection Molding
Z:\Zimmwriter\HighOutput_Injection_Molding_Services_0006.jpg
What production volumes can be considered realistic for high-volume injection molding? Typically, a production run exceeding 10,000 units is often regarded as high-volume, with many manufacturers aiming for hundreds of thousands or even millions of parts.
The feasibility of such volumes hinges on several design considerations, including part complexity, material selection, and mold design intricacies.
High-volume injection molding is characterized by repetitive processes that necessitate optimized designs to guarantee consistent quality and efficiency. Molds must be engineered for durability, capable of withstanding extensive cycles while maintaining tight tolerances.
Additionally, the selection of materials influences both the speed of production and the final part performance, necessitating a thorough analysis during the design phase.
Moreover, the production environment must be strategically designed to facilitate rapid cycle times without compromising quality control. Automation and advanced technological solutions, such as real-time monitoring systems, can further enhance productivity, allowing manufacturers to meet ambitious production targets.
Ultimately, realistic production volumes for high-volume injection molding are contingent upon meticulous planning and innovative design strategies that align with market demands and operational capabilities.
Conclusion
To conclude, high-output injection molding services serve as the backbone of modern manufacturing, transforming raw materials into intricately designed components with remarkable efficiency. Like a well-oiled machine, these services facilitate the rapid production of high-quality plastic parts, meeting the relentless demands of various industries. As technological advancements continue to enhance capabilities, the landscape of injection molding evolves, enabling businesses to navigate market challenges and seize new opportunities with agility and precision.